![]() |
Careful planning and close collaboration with suppliers are key elements in achieving effective plant maintenance, according to a leading UK industrial laundry firm.
Berendsen UK Ltd, part of the Elis S.A. group, an international provider of textile, hygiene and facilities services across Europe and Latin America, outlines why this approach provides the building blocks for effective plant maintenance.
Plant maintenance is always an area of business that needs to be handled carefully. “While you have to factor in a certain amount of planned and unplanned maintenance, the aim is always to have your machines working as close to 100% of the time as you can,” explains Barry Quinn, Engineering Manager at Berendsen. “A good plant-maintenance strategy is essential for us – any downtime has a direct impact on the bottom line, so you need to be set up so that both planned and unplanned maintenance has as little impact to your daily operations as possible.”
Be prepared
Planned maintenance, as the name suggests, comes down to organisation, according to Quinn. “You need to firstly identify the best time to do the work and where it will have least impact on your productivity,” he says. “Then you need to make sure that you will have the parts required – we work with RS who ensure we have everything we need, when we need it.”
When it comes to unplanned maintenance, however, the secret is preparation. Berendsen relies on a huge number of machines across its 60 sites, and unplanned downtime has a direct impact on productivity for each of these operations, so Barry has implemented three initiatives to help reduce downtime.
"We rely on RS's knowledge to make everything run smoothly" Barry Quinn, Engineering manager, Berendsen
Firstly, the company uses a clear priority system based on which machine is not working and how critical it is to productivity. “If a boiler goes down then the whole site is down, so that is of the utmost priority,” says Quinn. “A single machine in a line of six still needs to be fixed within a few hours, but is not as business critical.”
Next, the number of engineers on duty has been doubled. “We have a minimum of two on site per shift,” Quinn adds. “Quite simply, two engineers can usually fix a problem more quickly than one, and it’s also not unknown for more than one machine to go wrong at the same time, so this has proven to be very useful.”
Finally, Berendsen works very closely with key suppliers to lean on their knowledge and insight so that replacement parts are available as and when they are needed. In the case of RS, Berendsen makes use of the company’s ScanStock system.
“After an initial meeting, our team would look at the organisation’s recent stock ordering history and what they use,” says Grace Skewis, RS Scanstock Representative “We would then look at how those orders affect their planned maintenance. We will also closely monitor these orders on an ongoing basis to provide data. We use that data to offer a reporting service, where we review with the customer the stock they have on hold and whether it’s still needed. Working together and providing current data allows us to adjust stock min/max levels as appropriate for their changing needs.
“The end goal is to be in a position to sit with a customer and look at what work they have coming up on site, with planned maintenance, and we can make sure that everything they need for that is in place and will be delivered in good time. It helps make the process much smoother and reduces the risk of maintenance taking longer than planned.”
The system also has benefits when it comes to unplanned maintenance, as Quinn found earlier this year. “We use the data from RS to adjust our stock levels and avoid holding unnecessary parts or add additional parts that are critical to keeping key machines running,” he says. “We had a major issue recently where several machines went down and needed a number of the same parts, but thanks to ScanStock, we had the right number on site and avoided a lengthy delay in getting everything up and running again.”
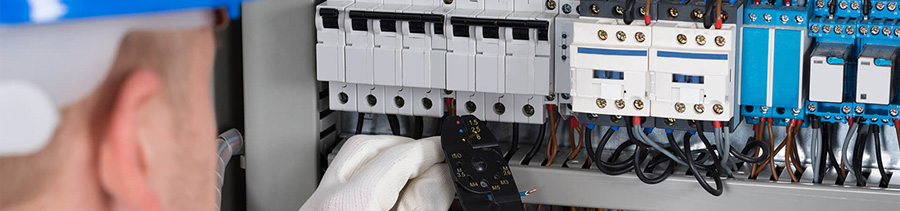
Look to collaborate
Skewis and Quinn agree that collaboration between a business and its suppliers is crucial when it comes to effective plant maintenance. “We look at RS and our other suppliers as partners,” says Quinn. “We work together to make sure that our machines are always online. We rely on RS’ knowledge to make everything run smoothly.”
Skewis adds: “We need to work with the customer as part of a team. I spend time with my customers and get to know their business so that I can give them advice that benefits them. For example, if a customer orders a certain part once every six months, this could be a low usage item but a critical spare. We would keep two in stock and only re-order when one is used – this ensures that we have a spare part at all times in the event of an emergency and re-stock only as required.
“It may sound simple, but it’s these sort of steps that avoid unnecessary downtime,” she adds. “At the end of the day, work with your suppliers and you will see the benefits.” - Grace Skewis, ScanStock Representative.
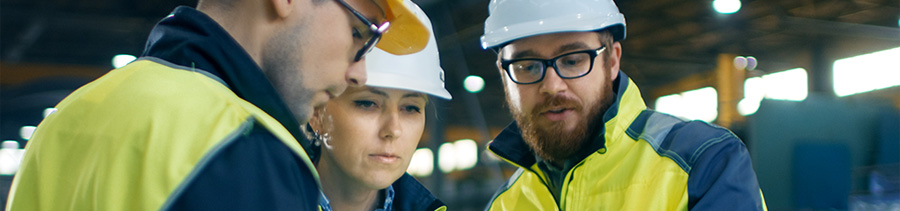
Identify the right solutions
It’s clear to see that the best approach for modern maintenance is a combination of planned and preventative measures, avoiding reactive maintenance whenever possible. There is a plethora of solutions available to help in this area: from handheld test and measure equipment that can be used by operatives to monitor variables such as pressure and temperature, to sensing products that monitor machine condition and alert operatives to potential issues. When it comes to smart solutions, the latest sensors allow integration with connected machines, with cloud computing platforms providing data to determine the health of the machine, enabling prediction of potential points of failure for breakdown. IoT will fast become the main element in the creation of an effective predictive maintenance strategy.
Making intelligent product selections can also help avoid breakdowns. Choosing to fit long-life bearings helps negate downtime, while ensuring you have the right lubrication is vital to obtaining the best operational life from mechanical systems. Investing in more advanced test and measurement such as motor analysers, thermal imagers and vibration analysers can help uncover unseen component degradation prior to the point of failure.
Keeping abreast of technology evolution and solutions, planning how best to structure and deploy maintenance teams, and ensuring the right parts are available when required are all critical to an effective maintenance strategy. Working with a knowledgeable distributor such as RS, which offers guidance material online, and works closely with leading brand specialists to advise on specific applications, will be invaluable for accessing the right products and knowledge to optimise a maintenance programme.
So What is ScanStock?
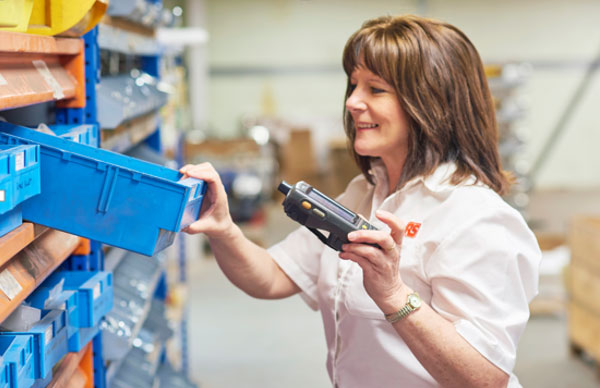
ScanStock is a managed inventory service that reduces the time & cost of replenishing low value, fast moving industrial supplies with our team managing it for you.
We manage everything, from the installation of storage solutions and barcoding software to regular stock checks and replenishment – allowing your team to focus on getting their job done.